Referenzen
Die Ergebnisse unserer Arbeit sprechen für sich. Entdecken Sie ausgewählte Projekte, die wir erfolgreich abgeschlossen haben.
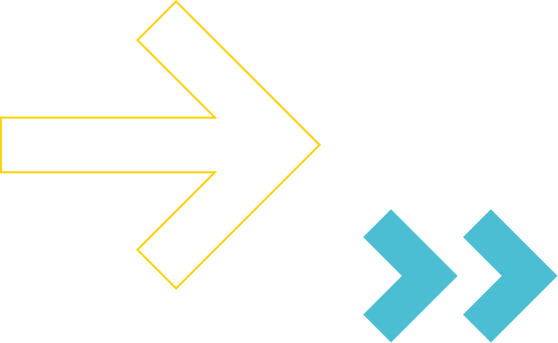
- 1800+
- Projekte weltweit
- 10
- Länder der Welt
- 8+
- Jahre auf dem Markt
Die Ergebnisse unserer Arbeit sprechen für sich. Entdecken Sie ausgewählte Projekte, die wir erfolgreich abgeschlossen haben.